Pneumatic components are vital to the operation of corrugation machinery, as they provide the necessary force and control to power various parts of the machine. These components, including Pneumatic Jacks, Solenoid Valves, Air Cylinders, and Connectors, help ensure smooth operation and precise control throughout the box-making process. In this blog, we’ll explore each of these key pneumatic components, highlighting their function and maintenance practices for corrugation and printing machines.
1. Pneumatic Jack (MTBL40X45CA-DC2 045B / 18-D-W)
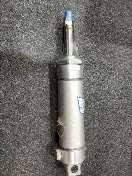
The Pneumatic Jack is a crucial component used to lift and support heavy parts of the corrugation machine, such as rollers, conveyors, and other key equipment. It operates by using compressed air to generate force, allowing for smooth movement and adjustment of heavy machine parts.
Maintenance Tips:
- Ensure the pneumatic jack is properly lubricated to maintain smooth functioning.
- Regularly inspect for leaks or pressure issues, which could affect the lifting ability.
- Check the seals for any wear and replace them if needed to prevent air loss.
2. Solenoid Valve (AC220V 4.5VA / Voltage Range AC187V-253V)
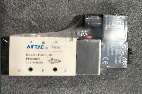
A Solenoid Valve controls the flow of compressed air in the pneumatic system. The Solenoid Valve (AC220V 4.5VA) is commonly used in corrugation machinery to direct air to various components like actuators, cylinders, and valves. It acts as the “switch” that either allows or blocks air, helping manage the movement and control of parts in the machine.
Maintenance Tips:
- Regularly check for dirt or debris that may clog the valve, causing it to malfunction.
- Inspect the solenoid coil for signs of wear or burnout and replace if necessary.
- Ensure that the electrical connections are clean and secure to avoid electrical failures.
3. Air Cylinders (SC 80 x 50, SC 63 x 75)
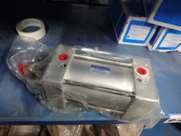
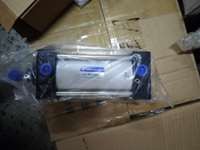
Air Cylinders (e.g., SC 80 x 50 and SC 63 x 75) are essential for providing the linear force needed for various movements in the machine, such as pushing, pulling, and lifting. These components rely on compressed air to extend and retract, performing tasks like sheet alignment or clamping.
Maintenance Tips:
- Regularly inspect for signs of leakage at the seals, as this can reduce efficiency.
- Clean the air cylinder regularly to remove dust or debris that might impair performance.
- Check the condition of the air filter to ensure it’s not clogged, as it can affect the cylinder’s performance.
4. Connectors (PC8-02, PCF8-02, PE 8)
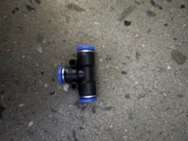
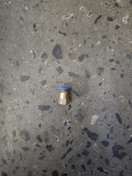
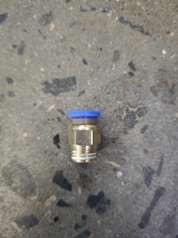
Connectors like PC8-02, PCF8-02, and PE 8 play an essential role in linking different pneumatic components together, ensuring that air flows correctly throughout the system. These connectors come in various sizes and are critical for maintaining the integrity of the pneumatic system.
Maintenance Tips:
- Inspect connectors for damage or wear that could lead to air leaks.
- Ensure that all connections are tight and secure, and replace any worn-out gaskets or seals.
- Clean the connectors regularly to prevent buildup that could obstruct the airflow.
5. Air Filters (AFC 2000, AFR 2000)
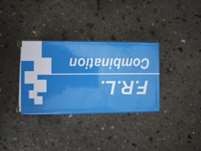
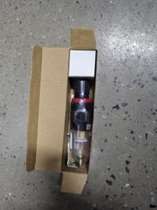
Air Filters like AFC 2000 and AFR 2000 are designed to clean the incoming air, preventing dirt, moisture, and other contaminants from entering the pneumatic system. Clean air is essential for preventing wear and tear on the pneumatic components, ensuring smooth and reliable operation.
Maintenance Tips:
- Regularly inspect and clean the filters to remove dirt and debris.
- Replace filters when they become too clogged to ensure the efficiency of the pneumatic system.
- Ensure that the filter is appropriately sized for your system to maintain optimal air quality.
6. Diaphragm (OD 124MM)
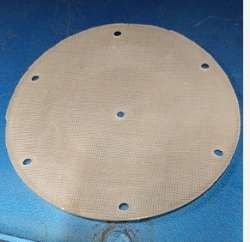
A Diaphragm is an essential part of many pneumatic components, including valves and actuators. It helps control the flow of air by flexing under pressure, allowing for smooth operation of various parts of the machine.
Maintenance Tips:
- Check the diaphragm for any cracks, tears, or wear, as this can lead to air leaks or malfunction.
- Replace diaphragms that show signs of damage or reduced flexibility.
- Ensure the surrounding components are well-maintained to reduce strain on the diaphragm.
Conclusion:
Pneumatic components are essential for the smooth functioning of corrugation machinery, providing the necessary force and control to perform various tasks. Pneumatic Jacks, Solenoid Valves, Air Cylinders, and Connectors all play critical roles in the operation of corrugating and printing machines. Proper maintenance, regular inspections, and timely replacements are key to ensuring that these components perform at their best, preventing downtime and increasing machine efficiency.
By following best practices for maintaining and troubleshooting your pneumatic components, you can extend the lifespan of your equipment and ensure smooth, high-quality production in your corrugated box-making process.